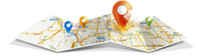
Address: No.139 GuoZhou Road Of High-tech Development,ZiBo City,ShanDong Province,China
Phone: 0533-8406588
Fax: 0533-8403717
Mail: sales@huaxiangwm.com
COMMON PROBLEMS AND ALUMINIUM WELDING WIRE WELDING TECHNIQUE
2019-07-22
Use the correct conductive mouth (inner diameter and length)
The longer the conductive mouth, wire feeding effect is best, conductive mouth diameter should be 10% larger than the diameter of a wire.
Maintain proper dust cover and conductive mouth relations
Conductive mouth should be concave inside the dust cover, from the dust cover distance from about 1/16 of an inch (1.6 mm) to the largest 1/4 inch
Use of the straight type nozzle welding torch or choose the goose neck
Choose straight type welding torch need to wire feeding wheel pressure.
Using nonmetal (teflon/nylon) input and output leads the mouth
Using U transmission wheel
Other types of wire feeding wheel would twist wire break the arc or scraping leading to produce more fire back. Sure U wheel has been to Angle instead of sharp edges.
Will guide wheel is arranged on a straight line
Improper arrangement godet wheel or pressure too high can cause distortion welding wire, wire feeding problems.
Check whether there is water gas leaks
Used in the teflon hose, don't put the pipe and the exchange use inch cushion gas hose.
Use the appropriate power supply
Welding equipment has many types, so want to choose the suitable for aluminum alloy welding machines and related accessories.
Don't crimp or bending conductive mouth
Use of conductive mouth can effectively reduce the conductive mouth straight accumulation and conductive mouth of arc.
In the event of a fire back before, need to clear all wire feed tube and wire
If it is found that wire to beat or spiral phenomenon, need to change a new conductive mouth, electric conductive mouth diameter or polishing
Use from a circular blade, the inner diameter of the new conductive mouth even if used conductive mouth will finished.
Appropriate protection and storage of welding wire
Don't for the night, the wire on the wire feeding machine is best stored in a temperature and humidity control box, relative humidity must be less than 30%.